The Real Meaning of Metal Cleanliness: Why Surface Prep Is More Than Skin Deep
Walk into any fabrication shop, automotive garage, or restoration facility, and you’ll hear a common phrase: “This metal’s clean.” But what does “clean” really mean? Is it simply free of visible dirt and rust? Or does true cleanliness require something deeper — something only modern technology like a laser metal cleaner can provide?
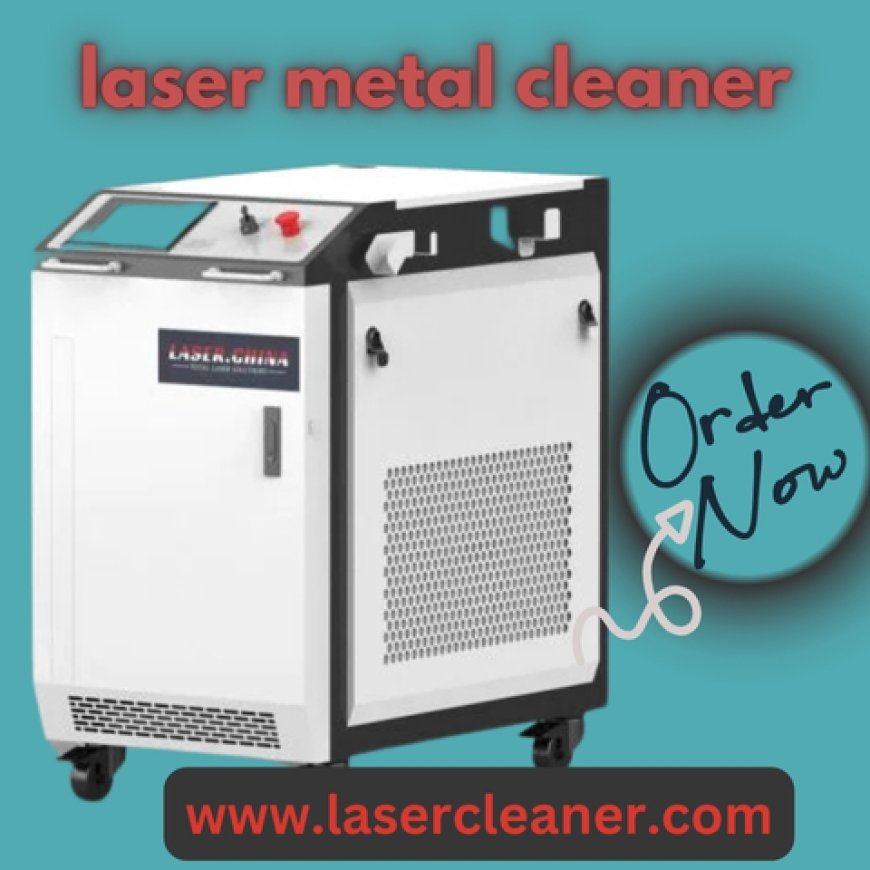
Let’s uncover what most traditional methods miss, and why surface integrity is at the heart of every successful weld, coat, or bond. If you're still relying on sandpaper, grinders, or chemical baths, you may not be cleaning — you're merely shifting the problem.
In this guide, we’ll explore how the laser metal cleaner has become the go-to method for surface preparation across industries.
What Lies Beneath: The Unseen Layers on Metal Surfaces
Before we dig into cleaning methods, it’s important to understand the makeup of contaminants on metal. Surface grime often appears simple — dust, grease, or rust — but most metals develop micro-oxidation, embedded residues, and thermal discoloration that are invisible to the eye. These layers:
-
Impede conductivity
-
Weaken weld joints
-
Cause coating failures
-
Accelerate corrosion
No matter how skilled the welder or painter is, a poor foundation guarantees failure. That’s where the laser metal cleaner stands apart. It doesn’t just “clean” — it prepares, restores, and revitalizes metal from the surface inward.
The Science Behind the Beam
The technology behind a laser metal cleaner is surprisingly straightforward in principle: a high-intensity laser beam is directed onto the metal surface, instantly vaporizing contaminants without harming the underlying material.
But what truly sets it apart is its precision. Unlike abrasives or chemicals, the laser can be adjusted by wavelength, pulse duration, and power level to target only unwanted layers. It’s like removing a sticker without leaving glue behind — a level of control other methods can’t match.
Real-World Applications That Rely on Laser Metal Cleaners
1. Automotive Restoration
Vintage car restorers swear by the laser metal cleaner. Why? Because classic vehicles are often covered in decades-old rust, paint, or body filler. Conventional sanding can eat into original panels, reducing value. Lasers allow restorers to clean precisely, preserving the integrity of rare components.
2. Aerospace Manufacturing
Precision is non-negotiable in aerospace. Surface prep before bonding or coating must meet tight tolerance standards. A laser metal cleaner ensures a contaminant-free surface without altering surface geometry — critical when dealing with lightweight alloys like titanium or aluminum.
3. Shipbuilding and Marine Repairs
Saltwater corrosion is ruthless. In shipyards, the challenge isn’t just removing rust, it’s doing so quickly and safely in damp, dirty environments. Lasers require no consumables, no abrasive media, and no drying time. Teams can clean large areas swiftly, reducing downtime.
4. Industrial Maintenance
Factories, oil rigs, and heavy equipment operators use laser metal cleaners during shutdowns. Surfaces contaminated with oil, carbon deposits, or chemical residues can be cleaned in place — no need to dismantle machinery or dispose of hazardous waste afterward.
When “Clean Enough” Isn’t Clean At All
In industrial environments, surface prep is often rushed or treated as a secondary task. But countless failures trace back to that one overlooked step — welding over oxidation, painting over microscopic dust, or bonding over oil films.
That’s why modern quality assurance teams insist on laser metal cleaning prior to critical operations. The level of repeatability, speed, and consistency it delivers simply isn’t possible with outdated methods.
Imagine:
-
A high-voltage electrical panel where unclean contacts cause arcing.
-
A turbine blade whose coating peels mid-flight due to poor adhesion.
-
A bridge support where corrosion returns months after repainting.
All of these costly failures can be prevented by ensuring a clean metal surface — the kind only a laser can deliver.
Beyond Rust and Paint: Hidden Contaminants the Laser Finds
One of the biggest misconceptions is that laser metal cleaners are only for rust or old paint. In reality, they’re highly effective at removing:
-
Black oxide scales from heat-treated metals
-
Soot and carbon deposits from engine parts
-
Protective oils used during shipping or storage
-
Weld slag and splatter from manufacturing lines
Since the laser never physically touches the surface, there's no smearing, scratching, or grinding into the base material. That’s what makes it suitable even for high-purity metals used in electronics and medical devices.
From Manual to Automated: Laser Cleaning at Scale
What began as a handheld tool for technicians has evolved. Today’s laser metal cleaner systems are integrated into robotic arms, CNC lines, and smart factories. Equipped with sensors, they can:
-
Detect and identify surface irregularities
-
Adjust cleaning patterns automatically
-
Log data for compliance and quality audits
This transformation makes laser cleaning not just effective, but traceable — a critical requirement in sectors like defense, nuclear, and aerospace.
Cost Isn’t the Barrier — Misconception Is
Many businesses delay investing in laser cleaning because of outdated assumptions: “Too expensive.” “Too complicated.” “Only for large companies.”
Here’s the reality:
-
Entry-level laser metal cleaners now come in portable, plug-and-play formats.
-
Training can be completed in under a day.
-
Over time, savings on consumables (chemicals, abrasives) offset the upfront cost.
Moreover, the real cost of sticking to traditional methods lies in downtime, rework, and safety risks. Once operators see the efficiency and cleanliness of laser prep, there’s usually no turning back.
Final Thoughts
When it comes to metal, what you don’t see can hurt you. Invisible contaminants weaken your work, sabotage durability, and erode your reputation. Whether you're welding, coating, bonding, or restoring, the foundation must be flawless.
A laser metal cleaner isn’t just a cleaning tool — it's a surface preparation solution built for precision, safety, and long-term performance. It aligns with the standards of industries that cannot afford failure, and it's now accessible to even small workshops.