The Future of Surface Restoration with LaserCleaner: A Game-Changer in Rust Removal
In industries where precision, speed, and cleanliness are crucial, traditional methods of rust removal are quickly becoming outdated.
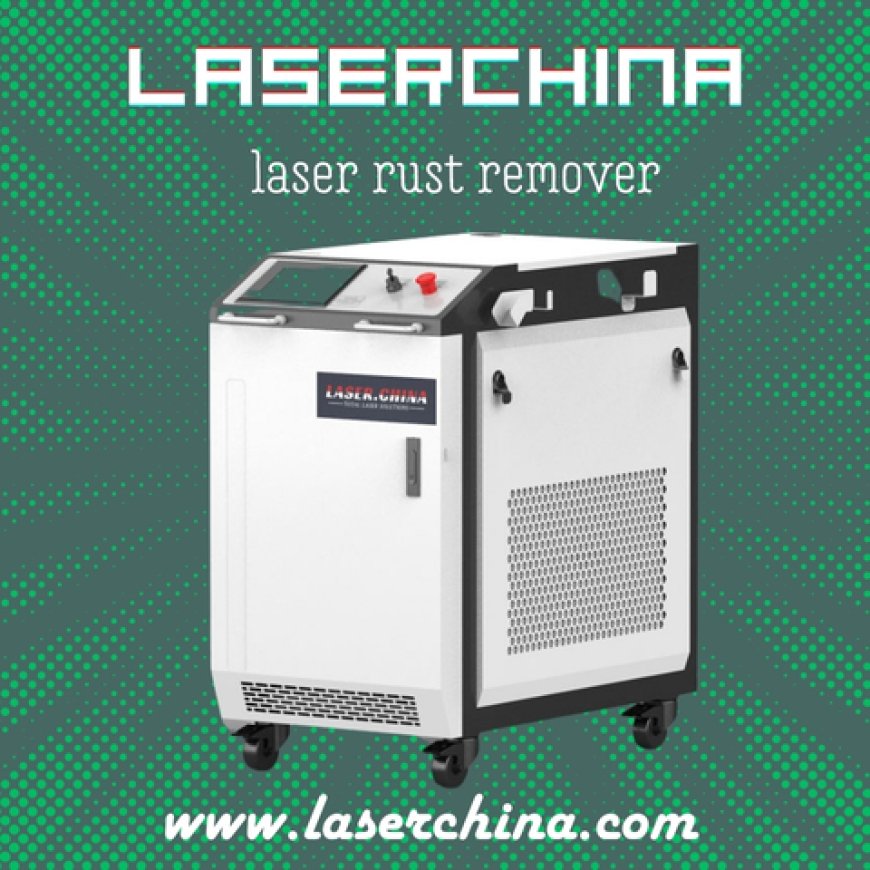
In industries where precision, speed, and cleanliness are crucial, traditional methods of rust removal are quickly becoming outdated. Sandblasting, chemical stripping, and abrasive methods, while effective, often come with significant drawbacks—such as damage to the base material, environmental hazards, and high maintenance costs. Fortunately, a cutting-edge alternative is reshaping how professionals approach surface treatment: the laser rust remover.
LaserCleaner is leading this technological shift, offering an advanced solution that combines efficiency, eco-friendliness, and surface preservation. Whether in automotive restoration, shipbuilding, aerospace, or historical conservation, this laser-based method is proving to be an indispensable tool for modern applications.
What Makes LaserCleaner Stand Out?
LaserCleaner’s technology is designed to remove rust, paint, oxide, oil, and other surface contaminants without damaging the underlying material. Unlike traditional cleaning tools, the laser rust remover doesn’t rely on physical contact or harsh chemicals. Instead, it uses a high-energy laser beam to break the molecular bonds of contaminants on the surface. This process results in minimal waste and maximum accuracy.
Additionally, LaserCleaner systems are highly customizable. Operators can adjust laser intensity and frequency based on the type of material and degree of contamination. From delicate antique metals to industrial-grade steel components, LaserCleaner provides a versatile, non-invasive solution.
Efficiency and Environmental Impact
One of the strongest advantages of using a laser rust remover is the minimal environmental impact. Traditional rust removal techniques often produce large amounts of dust, chemical waste, and secondary pollutants. LaserCleaner, by contrast, produces virtually no residue aside from vaporized particles, which can be easily extracted using filtration systems.
This makes LaserCleaner not just an effective solution, but a sustainable one as well. Businesses looking to meet stricter environmental compliance standards or reduce their carbon footprint will find this an ideal alternative. Furthermore, because the process is contact-free, the risk of tool wear and subsequent maintenance is drastically reduced—resulting in lower operational costs over time.
Precision for Demanding Industries
In fields such as aerospace and medical manufacturing, precision is not a luxury—it’s a requirement. LaserCleaner technology is capable of targeting extremely small areas with millimeter-level control, allowing technicians to clean surfaces without affecting neighboring sections. This is particularly useful in maintenance scenarios where specific components must be cleaned in situ without dismantling complex assemblies.
Moreover, the controlled nature of laser cleaning minimizes heat input, which is crucial when working with sensitive or thin materials. The absence of mechanical force also means there is no deformation, scratching, or warping of the surface—an essential factor in high-tolerance environments.
Why Professionals Choose LaserCleaner
For professionals seeking a reliable and efficient laser rust remover, LaserCleaner provides an all-in-one solution. Whether restoring corroded parts, preparing surfaces for welding, or cleaning production equipment, the system delivers a consistent and repeatable outcome. The equipment is portable, user-friendly, and requires minimal training, making it suitable for both large-scale industrial use and specialized, small-batch jobs.
Those looking to invest in this transformative technology can learn more through LaserCleaner’s official platform, where they can explore models, applications, and technical details about integrating laser-based cleaning into their operations.