Common Quality Control Problems in Custom Candy Box Production
Valve through the major obstacles of quality control in custom candy boxes manufacturing and present methods to preserve brand integrity.
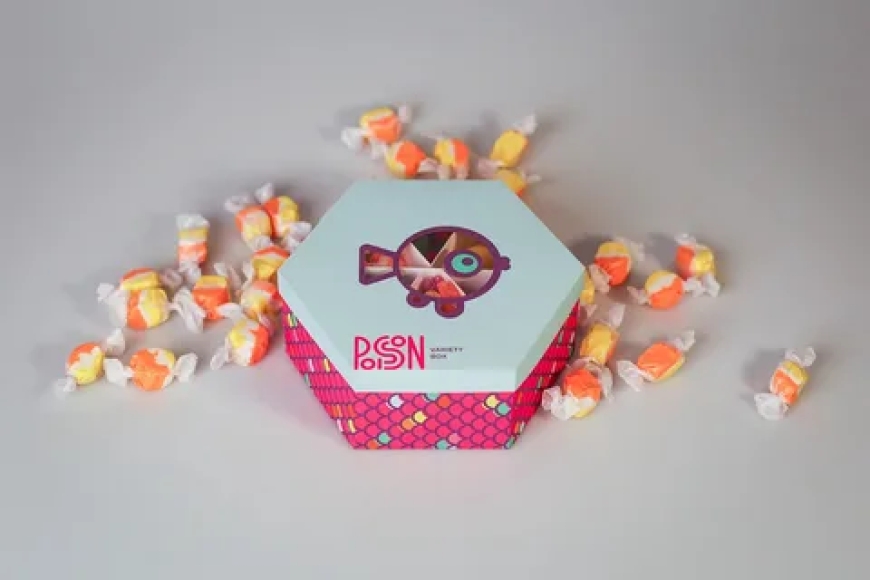
Packaging has an essential position in candy marketing competitions because it forms a critical component that influences how consumers choose their purchases. Candy boxes possess more meaning than their functional role because they outline both the brand values and product quality of your company. Packaging quality control presents a fundamental need for custom candy boxes because it ensures product safety together with pleasing design.
Products that fail to satisfy quality norms create unhappy customers and harm products and lead to decreased brand trust. Your product will see a negative impact on shelf perception due to such flaws as inconsistent prints along with structural failures. This blog exposes typical defects that manufacturers experience during custom candy box manufacturing and presents solutions that can prevent them.
Misalignment in Design Printing
Printing misalignment occurs as one of the main quality problems during candy box manufacturing. Slight errors in any logo design or graphics and branding elements result in an unprofessional box appearance. Your brand image suffers when you use custom candy boxes with logos since poor alignment leaves a negative impact on the market.
The quality of design templates and equipment calibration determines the final position of printed materials. Each printer and piece of equipment requires constant maintenance and inspections, which guarantee their precise performance. The perfect appearance of a candy box expected by customers will instantly disappear if they encounter hazy or poor print alignment.
Weak Structural Integrity and Material Flaws
Physical durability of boxes constitutes a regular problem among manufacturers. Candy boxes experience shipping damage because their designs lack quality and their construction materials fail to meet industry standards. The wholesale packaging of candy boxes results in weakened strength of individual units since bulk formats cause structural issues.
Cardboard thickness choices and materials used for lamination while corner reinforcement methods determine the stability of the product box. A quality-made candy container needs to safeguard its contents as well as maintain original dimensions and visual attractiveness during all stages of delivery and movement.
Inconsistency in Sizing and Die-Cutting
Consistency represents the essential element for packaging operations. Poor die-cutting processes combined with irregular package dimensions create three critical problems: loose candy inside the box, mismatched lids, and improperly closed packaging. The lack of precision during manufacturing custom candy boxes in canada creates embarrassment among companies that focus on high standard quality and accuracy requirements from their customers.
Your shipping expenses and distribution processes will suffer when your products have irregular dimensions since they create challenges in package delivery operations. Using advanced precision die-cutting equipment with regular quality assessment operations produces consistent dimensions throughout every manufacturing production run.
Color Variation Across Batches
The consistency of colors holds equivalent importance as structural packaging characteristics. Customers anticipate the brand colors to stay constant whether they buy products at different times or locations. When the ink quality suffers or printers use flawed settings or materials diverge from one another, then visible color alterations become apparent. The variation in appearance will negatively affect designs that require a specific theme, such as Valentine's candy boxes.
Brand trust suffers from such color inconsistencies since these variations create confusion among consumers. Production teams who follow certified Pantone color systems with strict color-matching protocols successfully decrease these color problems.
Improper Closure Mechanisms
Custom-printed box production encounters a major obstacle when closure failure occurs unnoticed. Any issue with flaps that refuse to close properly or with misaligned magnetic lids simultaneously damages functionality and appearance of custom items. The issue becomes particularly difficult to handle when it comes to gift candy boxes because presentation quality stands as the most important factor.
An improperly closing box poses a higher risk of spilling its contents because it will not stay secured during transportation. The proper assessment of all closure types should include tuck ends alongside magnets and snap locks as fundamental quality control procedures.
Overlooking Customization Errors
Packaging companies offer custom solutions including brand elements to messages alongside personalized names for candy packaging in present-day markets. When personalization is not monitored closely it can lead to unwanted errors in finished products. Brand image suffers from carelessness when the packaging contains wrong names alongside poorly spelled words or off-placement of graphics. The problem affects personalized candy boxes because each box receives personalized content.
QC teams must examine each point of detail while performing their duties, especially for variable data printing sessions. The use of automated verification systems reduces the number of mistakes that occur during customized production processes.
Flawed Finishing and Coating Techniques
Any package attains its final appeal from applying gloss, matte, UV spot, or embossing finishes. The outcome suffers from adverse effects, including peeling and bubbling, when the finishing process is done hastily or incorrectly. Surface appearance plays a vital role in purchase decisions for candy box packaging products, thus making poor finishing a significant problem.
The overall visual appeal decreases together with the durability of the box against water exposure because of inadequate finishing methods. Manufacturers need to use prolonged drying high-quality coatings and perform adhesion tests during their quality control procedures.
Conclusion
Any flaws in the quality control process of custom candy box manufacturing will either strengthen or weaken your brand image in the market. Putting customer faith together with brand loyalty diminishes because of printing and structural flaws present in each instance. Competitive businesses should spend on dependable materials alongside skilled personnel and modern technology to minimize such recurrent quality risks.
Your packaging creates the initial contact between customers and your brand as they see it for the first time. The correct application transforms the basic candy container into a brand experience that customers will remember. Proactively fixing these quality control problems helps you deliver your product exactly how it needs to be seen: funny, collected, and completely premium.